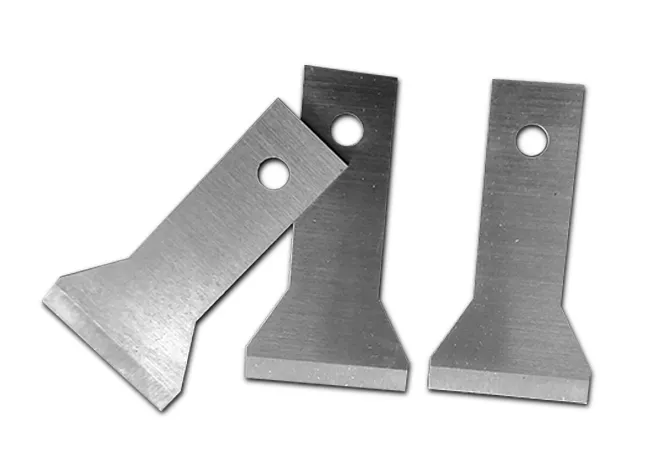
Plastic pelletizer knives play a crucial role in the plastic recycling and processing industry. As the demand for recycled materials continues to rise, the significance of efficient machinery, including pelletizers equipped with high-quality knives, becomes paramount. This Irregular Shaped Specialty Blades delves into the functionality, types, materials, and maintenance of plastic pelletizer knives, providing a comprehensive understanding of their role in modern manufacturing.
The Functionality of Plastic Pelletizer Knives
Plastic pelletizer knives are specifically designed to cut plastic materials into small, uniform pellets, which can then be used for various applications, including manufacturing new plastic products. The cutting process occurs within a pelletizing machine, where the knives work in conjunction with a rotating rotor and a stationary bed. The knives slice through the plastic material as it is fed into the machine, ensuring consistent pellet size and shape.
The efficiency of the cutting process is essential for maximizing productivity and minimizing material waste. Well-designed pelletizer knives can significantly impact the overall performance of the pelletizing machine, leading to better output and reduced energy consumption.
Types of Plastic Pelletizer Knives
There are several types of plastic pelletizer knives, each designed for specific applications and materials. The most common types include:
- Straight Knives: These knives are typically used for general-purpose cutting and are suitable for a wide range of plastic materials. They offer a simple design that provides efficient cutting performance.
- Circular Knives: Often employed in high-speed pelletizing applications, circular knives are designed to provide smooth and consistent cuts. Their shape allows for faster cutting speeds, making them ideal for processing large volumes of plastic.
- HSS (High-Speed Steel) Knives: Known for their durability and ability to maintain a sharp edge, HSS knives are commonly used in industrial applications. They are resistant to wear and can withstand the demands of continuous operation.
- Carbide Knives: These knives are made from tungsten carbide, offering exceptional hardness and wear resistance. They are ideal for processing abrasive materials and can significantly extend the life of the pelletizer knives.
- Specialty Knives: Some applications may require custom-designed knives tailored to specific materials or processes. Specialty knives can be designed to meet unique cutting requirements, ensuring optimal performance.
Materials Used in Plastic Pelletizer Knives
The choice of material for plastic pelletizer knives is crucial for their performance and longevity. Common materials include:
- High-Speed Steel (HSS): This material offers a good balance of hardness and toughness, making it suitable for general cutting applications.
- Carbide: Known for its hardness and wear resistance, carbide is ideal for processing tough and abrasive materials, though it may be more brittle than HSS.
- Stainless Steel: Used in applications where corrosion resistance is essential, stainless steel knives are often employed in environments with high humidity or exposure to chemicals.
- Tool Steel: This material is designed for durability and strength, providing excellent performance in demanding cutting applications.
Maintenance and Care for Pelletizer Knives
Proper maintenance of plastic pelletizer knives is essential to ensure optimal performance and longevity. Here are some best practices for maintaining these critical components:
- Regular Inspection: Routine checks for wear, damage, or dullness can help identify issues before they impact performance. Knives should be inspected for chips, cracks, or other signs of wear.
- Sharpening: Keeping knives sharp is crucial for efficient cutting. Dull knives can lead to increased energy consumption and lower output. Depending on the material being processed, sharpening may be needed more or less frequently.
- Cleaning: Regular cleaning of the knives and surrounding areas is essential to prevent the buildup of material that can affect performance. Cleaning agents should be chosen based on the materials being processed to avoid damage.
- Proper Alignment: Ensuring that knives are properly aligned within the pelletizing machine can prevent uneven wear and improve cutting efficiency.
- Replacement: Knowing when to replace knives is critical. Overly worn or damaged knives can lead to poor performance and increased operational costs.
The Future of Plastic Pelletizer Knives
As the plastic recycling industry continues to evolve, so too will the design and manufacturing of plastic pelletizer knives. Innovations in materials science and cutting technology will likely lead to knives that are more efficient, longer-lasting, and better suited for specific applications. Furthermore, with increasing emphasis on sustainability and reducing plastic waste, the demand for high-performance pelletizer knives is expected to grow.
Conclusion
Plastic pelletizer knives are essential components in the plastic recycling and processing industry, directly influencing the efficiency and quality of pellet production. Understanding the different types, materials, and maintenance practices associated with these knives is crucial for manufacturers looking to optimize their processes. As the industry continues to evolve, staying informed about advancements in knife technology will be key to maintaining a competitive edge in the market.